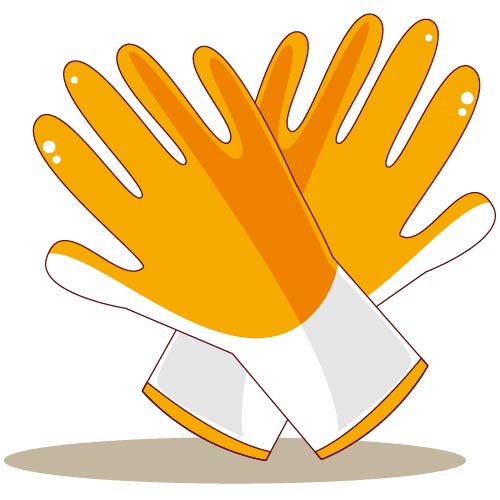
26 Oct A Handy Guide to Choosing the Right Gloves
By Safety Management Group
What’s the most common kind of workplace injury? The U.S. Department of Labor says that it’s injuries to the hand and fingers, which account for more than a quarter of recordable workplace injuries.
That’s important to know for two reasons. While working, we depend on our hands and fingers more than any other body part (except perhaps our eyes). Most of the tasks workers perform involve hands and fingers to some degree. The second reason is that injuries to hands and fingers are among the most preventable types of injuries.
One of the most familiar ways to protect hands and fingers is the use of gloves. However, simply telling a worker to wear gloves is an inadequate approach. There are many types of gloves, each with specific properties; therefore, it’s critical to match the type of glove to the task to be performed. Choosing the wrong type of glove could actually increase the potential for injury.
Types of injuries
Hand and finger injuries generally fall into one of three categories:
- Contact injuries are those that occur when hands and fingers come into contact with something dangerous, whether that’s an extreme temperature, some type of chemical, or a bloodborne pathogen.
- Traumatic injuries generally occur when hands and fingers are cut, pinched, punctured, and/or otherwise injured by tools or machinery.
- Repetitive injuries are those which result from repeated movements over a long time.
Gloves offer protection from contact and traumatic injuries by creating a barrier between the hands and fingers and the hazard.
If workers have access to gloves, why do so many injuries occur? In some cases, it’s because the worker is using the wrong type of glove for the hazard, or a glove that can’t perform its function properly because of damage. In other cases, it may be that workers believe the glove to be uncomfortable or interfering with the task and choose not to wear it. That’s why supervisors need to ensure that workers have access to gloves that are comfortable, functional, and provide the proper protection.
Which glove is right?
A key part of every safety program is assessing the potential hazards associated with the worksite and the specific task that will be performed.
Heat and cold: For hot work or tasks involving either very cold materials or cold environments, insulated gloves generally offer the best choice. If the worker will be close to a radiant heat source, an insulated glove made from reflective materials may be needed.
Chemicals: There are many types of gloves that may be suitable for working with chemicals. However, no single type is best for every type of chemical. It’s critical to understand the specific hazards associated with the chemicals and the various forms of those chemicals that the workers may encounter. Reviewing the Material Safety Data Sheet (MSDS) is a good starting point. Depending upon the nature of the chemical and the type of potential exposure (whether constant or incidental), rubber, vinyl, neoprene, or other gloves may be the best choice.
Dangerous surfaces: When workers have to handle sharp objects or surfaces that are jagged or rough, cut-resistant gloves made from metal mesh or thick leather will offer the greatest protection against cuts and punctures. In situations involving particularly sharp materials or cutting tools, workers may best be protected by gloves made from materials such as Kevlar® (which is also used in bulletproof vests).
Electricity: If the task may exposure the worker to electrical hazards such as shock, the best choice will likely be gloves made from insulating rubber materials.
Fire: If a worker may come in contact with open flame, fire-retardant gloves will provide the best protection.
Delicate materials: Sometimes, the purpose of the glove isn’t to protect the workers from the material, but to protect the material from the worker. An example of this is a workpiece that may be affected by oils in the skin. In these situations, gloves made from a soft material such as cotton may be optimal.
Enhancements
To improve the performance of the glove or to make it easier for the worker to perform a specific task, glove manufacturers may apply special coatings such as nitrile, latex, or polyurethane to gloves. Other enhancements such as vibration-reducing pads may be added to gloves for use in specific applications. Again, making the right choice depends largely upon the nature of the tasks to be performed.
Using gloves properly
Gloves can only provide the desired level of protection when they are not damaged. Even the most well-made glove may only provide a few days (or even a few hours) of performance in a heavy industrial setting. Before putting a pair of gloves on, the worker should inspect them carefully to ensure that there are no rips, tears, cracks, or any other kind of damage that could impair the protection. If any defects are found, the glove should be discarded immediately.
The gloves should be large enough to completely cover the worker’s hands. They should be tight enough that they won’t slip off inadvertently, but not so tight that they become uncomfortable.
Gloves worn for chemical resistance require additional attention. Before putting them on, workers should place bandages over any scrapes or cuts on their hands to ensure that chemicals won’t be able to come in contact if the glove fails. After working with chemicals, workers should rinse the gloves thoroughly, remove them without touching the exterior to their skin, and then wash their bare hands thoroughly using the proper type of cleaner. The gloves should be placed in a container so they can be decontaminated or disposed, depending upon the correct procedure.
Beyond gloves
In some cases, gloves alone cannot provide an adequate level of protection. For those situations, there are a variety of products that can be used in conjunction with gloves. One example is hand pads, which offer extra protection from surfaces that may be hot or unusually ragged. Thumb or finger guards may be added when the potential for injury is greater than normal. When working with chemicals or unusually high heat, clothing with long cuffs may protect the wrist and lower arms. Finally, when a worker cannot use gloves for some reason, there are barrier creams that may be applied to the skin to offer some degree of protection.
The Safety Management Group is a nationally recognized professional service organization that provides workplace safety consulting, training, staffing, program planning, and implementation. Visit them online at www.safetymanagementgroup.com.
Sorry, the comment form is closed at this time.